Microfabrication Facility

The Microfabrication Facility provides space, equipment, and assistance to design and manufacture devices for several groups within the institute and for other research institutions. The clean room (35 m2- Class 1000) is used to develop silicon masters via photo-lithography and it is equipped with a spin coater for deposing thin layers of SU- 8 photoresist, hotplates for baking the resist and two mask aligners (EVG-620, UV-KUB 3) for exposing the wafers to UV illumination. Structures with features of 7-10 micrometers can be fabricated and a white light interferometer (Wyko NT1100) is used to accurately measure film thickness, surface roughness and surface features.
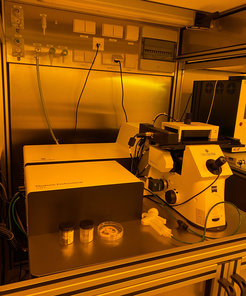
Microfluidic devices are assembled outside of the clean room environment after replica molding of the fabricated silicon master. The facility is also equipped with a 3D laser lithography system (Photonic Professional GT) used to build unique 3D structures and devices with submicron resolution. Starting from the CAD model of the structure, using embedded software it is possible to rapidly print the structures with high degree of complexity via two photon polymerization of a UV curable photoresist.
Beside lithography, a high precision milling machine (DMU 50, DMG Mori Seiki) is used to pattern microchannels in hard plastic and metals for fabricating structures from 150 microns up to 10 cm.
The facility plays a pivotal role in developing microfluidic platforms for generating compartments that mimic cellular systems within the Max Planck Network on Synthetic Biology (MaxSynBio/cors), a joint Max-Planck-BMBF initiative. Training and assistance in microfabrication at all levels, from design to the use of microfluidic devices, is provided by the facility
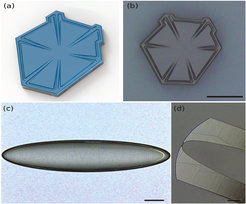